Die Casting Process for Making Automotive Parts
There are two basic die casting processes for manufacturing automotive components – hot chamber and cold chamber die casting machines. The process you choose will depend on your material choice, size, geometry, and complexity.
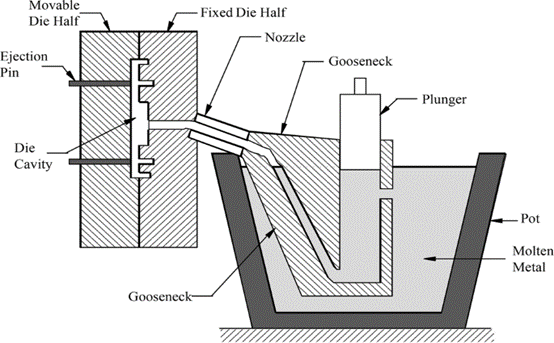
The hot chamber die casting process is sometimes called hot die casting. The gooseneck machines used in this process have built-in furnaces that heat the metal up until it gets molten. A hydraulic-powered piston forces the molten metal from the furnace into the die cavity using the nozzle and the gooseneck. The molten metal is then held under pressure in the die cavity until it solidifies.
This type of die casting has an internal melting point. Therefore, it is best suited for metals with lower melting points. Aluminum’s melting point is 1,220 degrees Fahrenheit, making it unsuitable for this process. On the other hand, Zinc and Magnesium with relatively lower melting points are ideal for this process.
Hot chamber die casting offers a fast production rate with over 18,000 shots per hour for small automotive die cast components. It melts metals within the casting machine, producing minimal material waste. Since it is a low melting point process, there is a longer die life, helping to save overall die casting cost. However, it is only cost-effective for high-volume productions. There is also low metal fluidity, thereby limiting products’ complexity.