Die Casting
This process involves pouring molten metal into the shot sleeve of the injection cylinder. After pouring, a hydraulic plunger forces the molten metal into the mold cavity without heating the sleeve. The pressure used in this process is between 30 Mpa and 150 Mpa. Since there’s no heat involved, the process is called cold chamber die casting. This process is ideal for high-melting-point aluminum alloys.
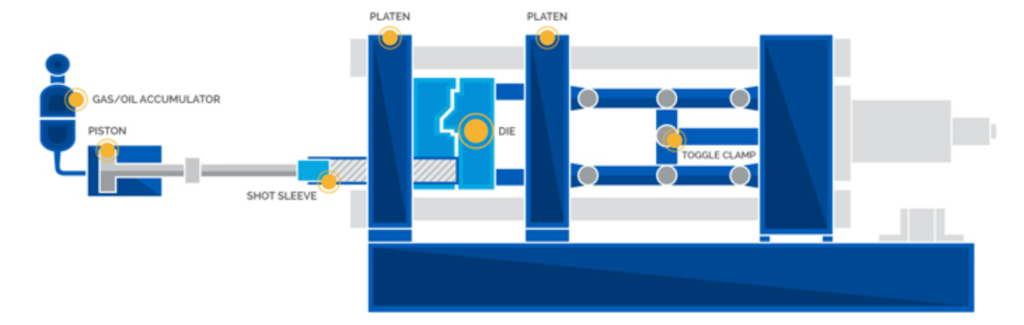
Cold chamber die casting offers exceptional dimensional accuracy to components. It also produces higher strength automotive parts and denser metal castings because of the increased pressure. The process is easy to carry out and requires lower maintenance costs. However, the cycle time is slower than the hot chamber process due to the transfer process. There are also possible high levels of contaminants that may affect the quality of the final auto parts.